How UKAS and ISO Accreditations Elevate UK Manufacturers in Innovation, Sustainability, and Excellence
March 17, 2025
UKAS and ISO Accreditations
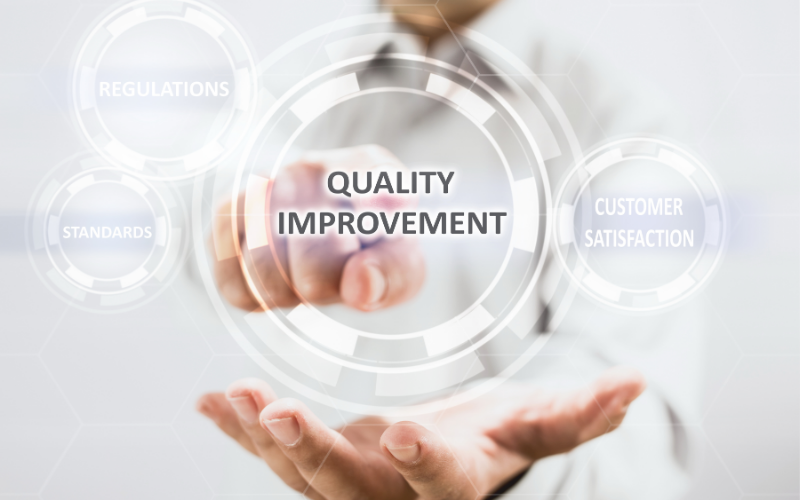
Welcome to the intricate world of standards and accreditations—a domain that might not seem exciting at first glance, yet we believe it holds the keys to trust, innovation, and sustainability within UK manufacturing. Have you ever wondered how some companies consistently deliver quality products while others struggle to keep pace? The answer often lies in something as seemingly mundane as industry standards.
Accreditations like UKAS and ISO serve as custodians of quality, consistently ensuring compliance, fostering innovation, and promoting competitiveness. For many manufacturers, these standards transform operations into well-oiled machines capable of extraordinary achievements.
UKAS (appointed by the government as the National Accreditation Body for the United Kingdom) accredits organisations that offer certification, validation and verification, testing, inspection, calibration, proficiency testing provision, reference material production, and imaging and physiological services against nationally and internationally recognised standards.
To be UKAS certified, an organisation must demonstrate accuracy of measurement, quality of raw materials, technical excellence, and skill in implementation, proving that what is being supplied meets the requirements specified or claimed.
“UKAS accreditation is associated with a 15% increase in market competitiveness for manufacturers"
Benefits of UKAS accreditation
More and more businesses are choosing to become accredited because of the opportunities and benefits that come with it.
Accreditation can:
- Assure the efficiency and validity of processes
- Confirm the accuracy of measurements
- Create assurance around innovation
- Demonstrate technical competence
- Prove impartiality
- Deliver confidence
- Gain commercial advantages
- Increase international acceptance for import & export
The International Standards Organisation (ISO) brings together global experts to agree on the best way to do things, from making a product to managing a process. As one of the oldest non-governmental international organisations, ISO has enabled trade and cooperation between people and companies worldwide since 1946. The International Standards published by ISO serve to make lives easier, safer, and better.
"Over 70% of UK manufacturers reported increased customer trust after obtaining ISO certification"
Benefits of ISO accreditation
- Organisations with ISO accreditation are considered to have improved efficiency, enhanced customer satisfaction, increased credibility, making it easier to access to new markets. The certification demonstrates a commitment to quality and continuous improvement.
- Research suggests businesses that follow ISO standards are more likely to improve their internal processes, resulting in cost savings and greater operational efficiency.
- Many UK companies report that achieving ISO certification has boosted their market reputation opening up new international trade opportunities.
UKAS and ISO often work together. Obtaining ISO certification is voluntary, whereas UKAS accreditation is crucial for demonstrating the credibility and recognition of your ISO certification.
Accreditations build trust
UKAS and ISO certificates represent our team's commitment to excellence. It's not just about prestige—they help us build trust and are a benchmark for that commitment.
Customers are increasingly prioritising quality and safety, and knowing our products meet stringent standards instils confidence. This trust translates into customer loyalty, fuelling repeat business and positive word-of-mouth.
Maximising the potential of our accreditations
Team Engagement:
Research shows that employees working under certified standards are often more motivated and demonstrate heightened pride in their work. We involve every level of our organisation in understanding what UKAS and ISO accreditations stand for to enhance product quality and boost morale.
Enhanced Innovation:
UKAS and ISO accreditations can drive innovation by acting as catalysts for maintaining and enhancing operational methodologies. By having standards in place to meet and exceed, our team is encouraged to think creatively to improve processes, reduce waste, and enhance productivity.
Competitive Boost:
We consider our UKAS certification more than compliance—it's a tool for differentiation that helps set us apart from our competition. Having UKAS and ISO accreditations signals to potential partners and clients that we walk the talk, demonstrating our proactive commitment to attaining and maintaining international standards.
Conclusion
Embracing UKAS and ISO accreditations isn't merely about fulfilling regulatory requirements. It's about setting a business apart, enhancing customer trust, and pioneering innovation within the competitive landscape of UK manufacturing. We are proud to be aligned with these prestigious standards; they demonstrate our commitment to quality standards and operational efficiency.
If you would like more information about our accreditations, please get in touch.
Footnote:
Pyroglass holds the UKAS and ISO Standards in high esteem and has recently received their official ISO9001:2015 external audit report from The British Assessment Bureau with a hattrick of zero scores for major and minor non-conformities and number of opportunities, and that's something every individual within the organisation is super proud of.
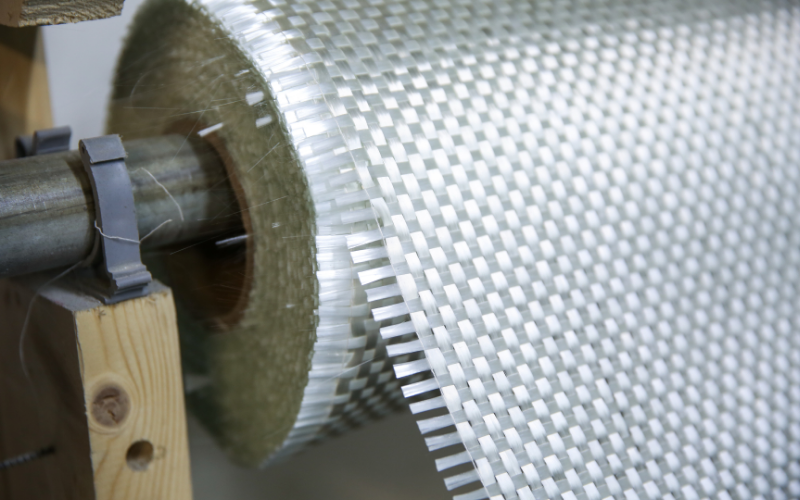
Sara Pullen, Managing Director of Pyroglass, invited me to the family owned independent organisation founded some 38 years ago. On entering Pyroglass, I was immediately impressed with the fine examples of glass fibre that adorned the walls throughout the building. Sara likes to tell people that Pyroglass is a knitting company, but as we open the doors of this Lancashire-based manufacturing plant, we discover there is a lot more to Pyroglass than meets the eye. Sara expanded, "We are in the business of knitting glass fibre that we use to produce a bespoke range of sealing and insulating materials capable of performing under extreme temperature conditions." I wanted to know more, so here is what I found out about the history of this exciting and innovative industry. Glass Fibre Knitting "Glass is an unlimited and innovative material that has plenty of applications. It is an essential component of numerous products we use daily, often without noticing. Glass continues offering cutting-edge solutions, including in combination with other materials. This trend is very likely to continue in the future". Source: Glass Alliance Europe When you think of knitting, what comes to mind? Sweaters, scarves and other clothing, right? Knitting is the process of making a textile by connecting loops or stitches of one continuous thread using needles. Pyroglass uses the same technique to produce knitted sweaters (by creating interlocking loops of yarn), but instead of wool they use texturised glass fibre yarns to form high temperature tapes, ropes and sleevings. Single glass fibres are very small (the largest being approximately one fifth of the diameter of a human hair ~9μm, each bundle of raw fibres may consist of thousands of individual fibres stranded together to form continuous fibre yarns which can be knitted. Glass fibre yarns have high tensile strength and can resist temperatures up to 550°C without losing structural integrity, making them an ideal component for many applications requiring high temperature sealing and insulation. "The Glass Industry in Europe is strong and diverse with 500 glass manufacturing plants, 500,000 jobs along the value chain, 25 European countries with glass production and 40 million tonnes of glass produced annually.” Source: Glass Alliance Europe Texturisation Process: Involves jetting streams of compressed air at the glass fibres, creating turbulence causing the formation of loops by overfeeding individual filaments which in turn mechanically bulks the strands. Texturising glass fibres improves thermal and acoustic insulation properties by creating air pockets within the stranded fibres, enhances the flexibility of the yarns so they can be knitted, increases the volume of the yarns for a “fluffier” finish and increases the abrasion resistance of the glass fibre. These features make texturised yarns particularly valuable in industries where high durability under heat stress is crucial, such as aerospace and automotive. High-Temperature Characteristics Glass fibre yarns are designed to withstand intense temperatures up to 550°C making them invaluable in industries requiring rigorous thermal management, such as automotive exhaust systems, aerospace engineering, fire-protective equipment, biomass boilers and incinerators. Safety and Reliability When exposed to such extreme temperatures, these glass fibre yarns maintain their tensile strength and flexibility, reducing the risk of failure in critical applications. This unique combination of properties places texturised glass fibre yarns in a category of their own when it comes to withstanding harsh environments. Cost Efficiency Longer lifespan in thermal environments means reduced replacement and maintenance costs. Incorporating texturised glass fibre yarns in your projects can enhance performance while ensuring safety and durability. It's a perfect example of how a seemingly simple innovation can have widespread, transformative impacts across many industries. The History of Fibreglass Venetian artisans used fine threads to adorn glassware in medieval times. Still, it was only during the Industrial Revolution that fine glass fibres were used for more reasons than just decoration. Here are some interesting facts I found from Science and Technology: 1836 , a Frenchman, Ignace Dubus-Bonnel, received the world's first patent for making glass fibres. 1842 saw a British silk weaver making a dress from glass fibre. 1872 , the Franklin Institute in Philadelphia reported that an engineer had produced "mineral cotton" by blowing a jet of steam through liquid glass, resulting in a white mass that could be suitable for insulating steam boilers and pipes. 1893 Edward D. Libbey of the Libbey Glass Company exhibited a fibreglass dress at the Chicago World's Fair weighing over 131 pounds (60kg). In the early 1900s, successful glass-blowing machines developed, helping to uncover the true potential of glass fibre. 1932 saw the first commercially successful product made from glass fibres, air filters for ventilating equipment that proved more capable of removing dust than cotton, especially popular with the increase in air conditioning equipment. But it was Slayter and Jack Thomas at Owens-Illinois who discovered a method of making glass wool for insulation. 1938 , Owens Illinois and Corning Glass joined forces and formed the Owens-Corning Fiberglas Corporation and subsequently produced a glass-wool insulation that was less expensive than mineral wool (or rock wool), making it the most popular insulating material of the time. Modern-day Applications of Glass Fibre In many ways, fibreglass acts like regular glass. It repels moisture; most acids and alkalis don't penetrate the filaments; it resists mould and mildew; it doesn't conduct electricity; it doesn't decay, rust, shrink, expand, or burn. Glass fibre is strong, solid and durable, making it ideal for many industries, including aviation, automotive, maritime and construction. Its non-combustible nature means it doesn't burn, smoke or emit toxic compounds when heated, which are characteristics important to the fire industry and domestic and industrial heating and cooking equipment. Glass fibre is a non-conductive and heat resistive material making it suitable for use around electrical components and wires, glass fibre is therefore an ideal component in numerous electrical and energy applications including solar, wind and PV systems, electrical components, insulators, housings etc. While glass fibre might seem like a new concept, its application in creating texturised yarns with high-temperature resistance has revolutionised numerous industries since the 1900s. Whether you're an industrial expert or someone curious about material science, understanding the development of glass fibre and its place in modern day industry allows us to appreciate innovations and their profound impact on technologies we encounter every day. Author: Lynne Rawlinson, Ribble Valley Marketing . Footnote: Pyroglass Limited was established in 1987 and remains an independently owned British manufacturing business with a wealth of experience in the design, production and marketing of specialist thermal materials. Pyroglass products are used worldwide for: • Domestic and Industrial Heating Equipment • Truck, Bus and Generator Exhaust Systems • Steel / Aluminium Smelting Plants • Hydraulic Hoses and Cable Systems • Cooking Equipment • Vehicle Electrical Wiring Harnesses • Oil Refineries and Oil Rigs • Thermal Acoustic Applications Please get in touch for more information on Pyroglass Knitted products.